What is Porosity in Welding: Comprehending Its Reasons and Enhancing Your Skills
What is Porosity in Welding: Comprehending Its Reasons and Enhancing Your Skills
Blog Article
Porosity in Welding: Identifying Common Issues and Implementing Finest Practices for Prevention
Porosity in welding is a pervasive problem that often goes unnoticed till it causes considerable issues with the integrity of welds. This common flaw can compromise the strength and resilience of bonded frameworks, presenting safety risks and bring about costly rework. By comprehending the source of porosity and applying effective prevention methods, welders can dramatically boost the quality and dependability of their welds. In this conversation, we will certainly discover the vital factors adding to porosity formation, examine its harmful impacts on weld efficiency, and discuss the best methods that can be adopted to minimize porosity incident in welding processes.
Common Reasons For Porosity
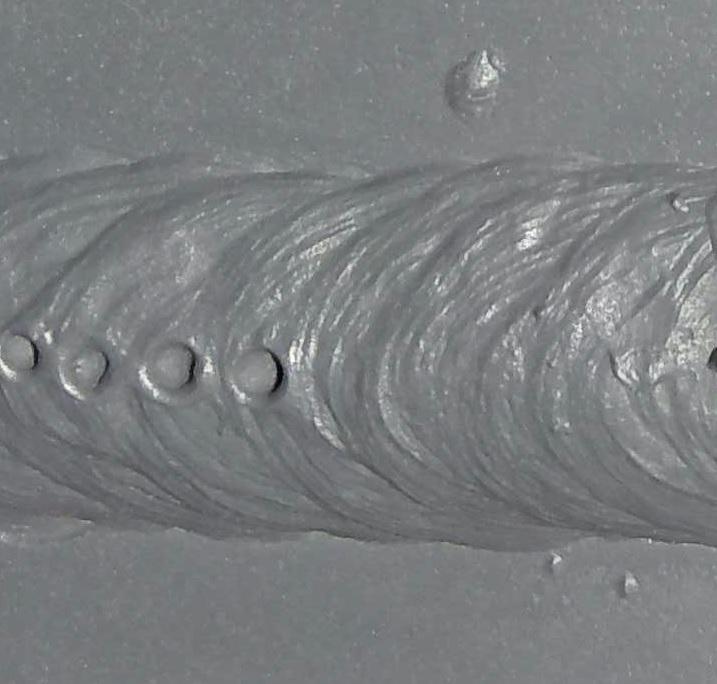
Using unclean or damp filler products can present pollutants right into the weld, adding to porosity concerns. To mitigate these typical causes of porosity, comprehensive cleaning of base steels, proper securing gas choice, and adherence to optimum welding parameters are important methods in accomplishing top quality, porosity-free welds.
Impact of Porosity on Weld Top Quality

The existence of porosity in welding can considerably compromise the structural honesty and mechanical homes of bonded joints. Porosity develops spaces within the weld metal, weakening its overall stamina and load-bearing capability.
Welds with high porosity degrees tend to exhibit lower effect toughness and reduced capacity to deform plastically prior to fracturing. Porosity can hinder the weld's ability to effectively transfer forces, leading to premature weld failure and prospective safety and security threats in important frameworks.
Best Practices for Porosity Prevention
To improve the architectural honesty and high quality of welded joints, what particular procedures can be applied to reduce the occurrence of porosity during the welding procedure? Using the you could look here proper welding technique for the specific material being welded, such as changing the welding angle and weapon position, can additionally protect against porosity. Regular examination of welds and prompt remediation of any issues recognized throughout the welding procedure are necessary methods to stop porosity and generate high-quality welds.
Importance of Proper Welding Techniques
Carrying out correct welding techniques is critical in ensuring the structural stability and top quality of welded joints, developing upon the foundation of reliable porosity avoidance procedures. Welding strategies directly affect the total stamina and durability of the welded framework. One essential element of appropriate welding strategies is preserving the proper warmth input. Extreme heat can lead to raised porosity as a result of the entrapment of gases in the weld swimming pool. Alternatively, inadequate heat might result in incomplete combination, producing prospective powerlessness in the joint. Additionally, making use of the ideal welding specifications, such as voltage, existing, and travel rate, is vital for accomplishing sound welds with marginal porosity.
In addition, the option of welding process, whether it be MIG, TIG, or stick welding, should align with the particular demands of the see this site project to ensure optimal results. Correct cleansing and preparation of the base metal, in addition to picking the right filler product, are also vital elements of competent welding methods. By adhering to these ideal methods, welders can minimize the threat of porosity formation and generate top notch, structurally audio welds.

Checking and Quality Assurance Measures
Checking treatments are crucial to spot and prevent porosity in welding, making certain the toughness and sturdiness of the final item. Non-destructive testing methods such as ultrasonic screening, radiographic testing, and aesthetic examination are frequently utilized to recognize prospective defects like porosity.
Post-weld inspections, on the various other hand, examine the last weld for any type of defects, including porosity, and validate that it meets specified standards. Carrying out an extensive top quality control strategy that consists of thorough screening procedures and inspections is vital to minimizing porosity issues and making sure the general top quality of bonded joints.
Conclusion
In conclusion, porosity in welding can be a typical issue that influences the quality of welds. By recognizing the typical root causes of porosity and executing best methods for prevention, such as appropriate welding methods and screening steps, welders can make sure high quality and trustworthy welds. It look at these guys is necessary to prioritize avoidance methods to decrease the event of porosity and preserve the stability of welded frameworks.
Report this page